Ensuring that your electrical, electronic, and electromechanical (EEE) equipment passes inspections is crucial for maintaining safety, performance, and compliance with legal standards. Whether you’re managing a manufacturing EEE inspection plant, running an office with specialized equipment, or overseeing an industrial operation, having a reliable checklist is essential for smooth inspections.
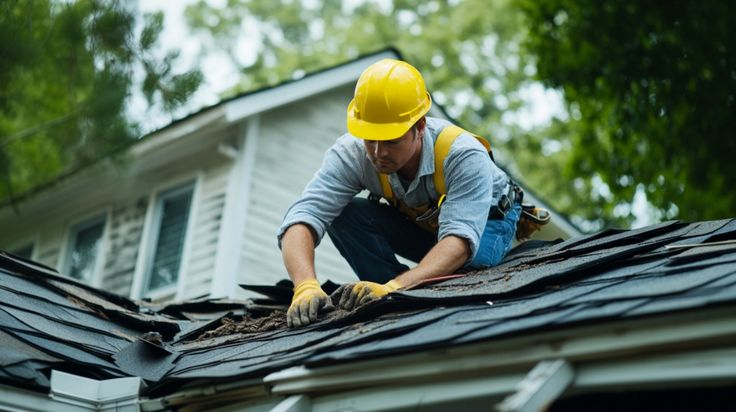
In this post, we’ll guide you through an EEE inspection checklist and provide practical tips to ensure your equipment passes inspections every time.
Why EEE Inspections Matter
EEE inspections are necessary for:
- Safety: Proper inspections ensure the safety of workers and prevent electrical hazards.
- Compliance: Following regulatory standards helps you avoid penalties and meet industry-specific guidelines.
- Efficiency: Regular inspection can prolong the life of equipment and reduce downtime from unexpected failures.
- Risk Mitigation: Identifying and addressing potential faults can prevent costly repairs or accidents.
Essential Components of the EEE Inspection Checklist
To make sure your equipment is ready for inspection, follow this checklist that covers the major components of any electrical, electronic, or electromechanical system:
1. Visual Inspection
Start with a simple but essential step—visual checks.
- Wiring and Cables: Inspect for wear, tear, or signs of overheating. Ensure no exposed wires are visible, and all cables are secured and free from any damage.
- Connectors: Check that connectors are securely attached and that there are no loose or frayed terminals.
- Signs of Overheating: Look for scorch marks, discoloration, or melted insulation around electrical components.
- Corrosion: Ensure that no parts are corroded, particularly for outdoor or high-humidity environments.
2. Electrical Safety Compliance
Electrical safety is critical for both personnel protection and the equipment’s longevity.
- Grounding: Ensure that all equipment is properly grounded to prevent electric shock and to safeguard against electrical faults.
- Circuit Breakers and Fuses: Check if circuit breakers and fuses are correctly rated, functional, and not tripped.
- Insulation Resistance Testing: Test insulation resistance to verify that no short circuits or leakage currents are present.
3. Functionality and Operational Tests
Testing the equipment’s operational capacity is another crucial step in ensuring it’s inspection-ready.
- Operational Tests: Verify the equipment works within its normal operational parameters (voltage, current, frequency).
- Performance Checks: Test the system under load to check for performance issues such as overheating or power surges.
- Control Systems: Ensure control switches, panels, and emergency stop functions are fully operational.
4. Environmental Considerations
Equipment that is exposed to harsh environments may have specific requirements for inspection.
- Dust and Moisture Protection: Check if the equipment is adequately protected against dust, moisture, or other environmental elements that could cause damage.
- Temperature Sensitivity: Ensure the equipment operates within the recommended temperature range, especially for sensitive components.
5. Documentation and Maintenance Records
Maintaining proper records is essential for tracking the health of your equipment and ensuring compliance.
- Inspection Logs: Keep detailed records of all inspections, including the date, inspector name, and any findings or corrective actions taken.
- Service and Maintenance Records: Have up-to-date records for any repairs, replacements, or maintenance performed on the equipment.
- Manufacturer Guidelines: Ensure that all inspections are conducted according to the manufacturer’s specifications, including any specific requirements for periodic checks or replacements.
6. Safety Precautions During Inspection
When conducting inspections, safety is paramount.
- Power Down: Always disconnect the power before beginning an inspection to avoid the risk of electrocution or injury.
- Personal Protective Equipment (PPE): Inspectors should wear appropriate PPE, including insulated gloves, safety glasses, and non-conductive footwear.
- Use of Proper Tools: Use insulated tools to minimize risk when working around live electrical components.
Tips to Ensure Equipment Passes Every Time
- Stay Up to Date with Regulations: Keep track of changes in local, regional, and national electrical safety codes and regulations to ensure your equipment meets current standards.
- Conduct Regular Maintenance: Don’t wait for an inspection to identify potential problems. Regular maintenance helps prevent issues from escalating.
- Train Your Team: Equip your team with the knowledge and skills to perform their own checks and troubleshoot minor issues before they become serious.
- Replace Aging Components: As equipment ages, parts wear out and may no longer function properly. Don’t hesitate to replace parts that show signs of wear or are nearing the end of their lifespan.
- Hire Professional Inspectors: If you’re unsure of your inspection skills or the complexity of the equipment, consider hiring a certified professional to ensure all safety and operational standards are met.
Final Thoughts
Ensuring your EEE equipment passes inspections every time requires diligence, routine checks, and an understanding of the inspection process. By following a comprehensive checklist, you can minimize risks, extend the life of your equipment, and stay in compliance with regulations.
Remember, a well-maintained system not only ensures safety but also boosts efficiency, helping your operation run smoothly without unnecessary delays or costs. Make inspection readiness a priority, and your equipment will thank you for it!